What is the Hidden Factory?
How Six Sigma Improves Efficiency and Quality Control
Six Sigma's "Hidden Factory" is the hidden world of waste and flaws that slows down production and lowers the quality of goods. Hidden issues like needless steps taken, overproduction, or errors that go uncorrected can deeply harm a factory's ability to produce. But just as shadows scatter when a bright light shines on them, Six Sigma techniques can reveal these hidden areas of waste, making it possible for them to be fixed. Imagine finding a secret room full of levers and dials controlling your operation, then turning them all towards efficiency – that's what unveiling the hidden factory can mean for a business. Now, let's talk about how to find these hidden levers.
Hidden Factory Definition: The hidden factory, within the context of efficiency and quality control, refers to a percentage of processing that occurs outside the established system of measurements. This hidden aspect often stems from root causes, prompting questions about the effectiveness of communication and collaboration among people within the organization. Identifying the hidden factory is crucial for implementing solutions that address underlying issues and enhance overall efficiency and quality control measures. By delving into the root causes and improving communication, organizations can uncover and rectify inefficiencies, ultimately optimizing their processes and improving product or service quality.
Six Sigma is a powerful methodology that uses statistical analysis and tools like DMAIC (Define, Measure, Analyze, Improve, Control) to systematically identify and eliminate defects or errors in production. By implementing Six Sigma, companies can uncover hidden inefficiencies within their manufacturing processes, leading to improved productivity, reduced waste, and increased customer satisfaction.
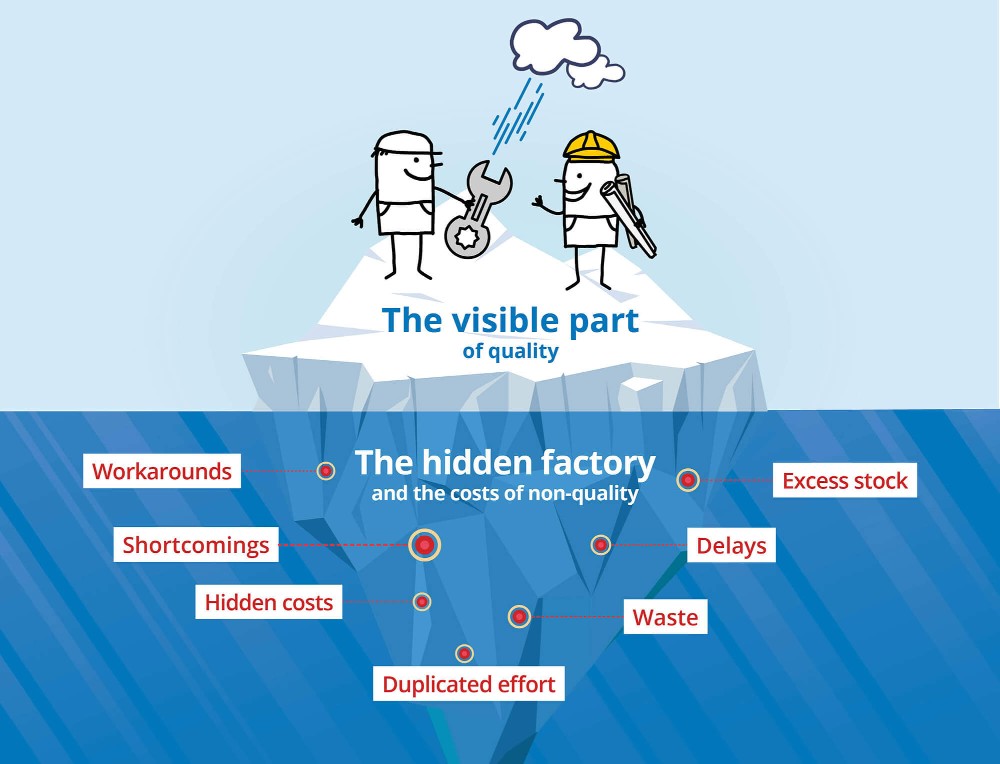
Six Sigma Hidden Factory
Unveiling the Six Sigma Hidden Factory
Imagine a bustling factory, but beneath its apparent productivity lies another factory—a hidden one. This hidden factory doesn't exist in a physical location; rather, it symbolizes all the wasted effort, resources, and time that go into production without adding any value. These can include defects, unnecessary processes, overproduction, and other inefficiencies that consume precious resources and hinder production flow.
In many cases, these issues go unnoticed or are overlooked because they blend into the day-to-day operations of a company. They gradually cause setbacks in productivity and quality. It's like having a room full of clutter that you don't see because you're so used to it. However, uncovering and addressing these hidden issues within the manufacturing process brings improved efficiency and reduced waste—similar to tidying up a messy room to bring clarity and order.
Consider a company manufacturing smartphones. In their drive to meet demand, they might produce more devices than needed, leading to excess inventory that ties up capital and storage space. Additionally, defects in some devices due to flaws in the manufacturing process may result in rework or customer returns, affecting overall customer satisfaction.
This is where Six Sigma comes in—the methodology serves as a powerful flashlight that illuminates every dark corner of the manufacturing process. By using tools like DMAIC (Define, Measure, Analyze, Improve, Control), companies can systematically identify and address these hidden issues. This structured approach enables companies to root out defects, streamline processes, and optimize production to deliver greater value to customers.
Understanding and addressing the concept of the Hidden Factory through Six Sigma allows companies to enhance their manufacturing process by eliminating waste, reducing defects, and ultimately increasing customer satisfaction.
By shining a light on the hidden inefficiencies in manufacturing, companies can now move forward to explore techniques of identifying these covert disruptions with precision and diligence.
What is the Six Sigma Hidden Factory?
The Hidden Factory is the set of activity (or activities) in the process that result in reduction of quality or efficiency of a business process or manufacturing department, and is not known to managers or others seeking to improve the process. Six Sigma focuses on identifying "hidden factory" activities to eliminate the root-causes.
One of the examples of Hidden Factory will be creating multiple versions of a status update presentation by the Project Management team because all of the requested information was not received by the due date from all the departments.
Six Sigma works effectively to identify the hidden factory situations, questions the status quo, removes it and thus it improves business profits and reduces wastes.
Techniques of Identifying Hidden Inefficiencies
Manufacturing processes can be quite intricate, with many interconnected steps and components. To identify and eliminate these hidden inefficiencies, Six Sigma uses specific techniques designed to pinpoint areas needing improvement. The goal is to streamline operations, reduce waste, and ultimately boost productivity.
Process Mapping
Process mapping is a valuable tool used to visually represent each step in the manufacturing process. Through creating flowcharts or diagrams, businesses gain a comprehensive understanding of the sequence of activities involved in production. This helps in identifying bottlenecks, redundant steps, and areas of waste. For example, it allows businesses to detect any repeated or extraneous steps that hinder efficiency.
Imagine process mapping as creating a detailed roadmap that illuminates every turn within a manufacturing process. This technique assists in discerning where the journey becomes arduous, indicating potential areas for optimization.
Value Stream Analysis
In addition to process mapping, value stream analysis is used to identify value-adding activities as well as areas of non-value-added activities or waste within the production process. This analysis provides a holistic view of the entire value stream, encompassing all activities from raw material acquisition to the delivery of the final product to customers.
Value stream analysis shines a light on core activities that contribute to transforming raw materials into finished goods and simultaneously exposes non-value-added activities or waste. By isolating such non-essential activities, businesses can streamline their processes and make them more efficient.
Data Analysis
Furthermore, Six Sigma leverages statistical tools and data analysis techniques to identify patterns and anomalies that indicate inefficiencies and areas for improvement in the manufacturing process. Through the careful examination of key performance indicators and relevant data points, businesses can uncover hidden patterns and trends that may otherwise go unnoticed.
Data analysis empowers organizations to move beyond mere conjecture regarding inefficiencies and engages with evidence-based insights. By diving into data patterns such as variations in production output or recurring defects, businesses gain valuable insights for making informed decisions about process improvements.
Through these meticulously designed techniques within the Six Sigma methodology, businesses can successfully uncover previously hidden inefficiencies within their manufacturing processes and pave the way for sustainable operational enhancements.
Process Improvement Strategies
In the realm of Six Sigma, specific methodologies and techniques are key players in enhancing the efficiency and quality control of the manufacturing process. Let's delve into some of these strategies.
DMAIC Methodology
The DMAIC framework—Define, Measure, Analyze, Improve, and Control—is an essential tool in the Six Sigma methodology. Let's break it down:
- Define: This first step involves identifying and defining the problem or inefficiency in detail. It sets the stage for the entire improvement process.
- Measure: The second step focuses on quantifying the extent of the problem using data and metrics. This step helps in understanding the current state of the process.
- Analyze: Once the problem is defined and measured, it's time to thoroughly analyze its root causes through advanced statistical tools and methods.
- Improve: Having identified the root causes, the next step involves implementing improvements or solutions aimed at addressing these root causes.
- Control: The final step focuses on maintaining the improvements over time by establishing controls and monitoring processes to prevent a possible reversion to the previous state.
The DMAIC methodology provides a structured approach to address issues methodically and ensure sustained improvements to the manufacturing process. By systematically following each phase, businesses can effectively identify, measure, analyze, improve, and control processes, leading to enhanced efficiency and reduced errors.
Error-Proofing Techniques
Another critical aspect of Six Sigma is the implementation of error-proofing techniques, also known as poka-yoke methods. Poka-yoke refers to designing processes or tools in a way that prevents defects from occurring in the first place. It essentially acts as a safety net for catching potential errors before they manifest into defects.
One classic example of error-proofing is found in automobile manufacturing, where parts are designed to fit together in only one way. This prevents assembly errors that could lead to larger problems down the line. Error-proofing is all about building in safeguards right at the source to reduce the need for rework or scrapping of products, ultimately leading to cost savings and improved overall quality.
Standardization of Processes
Standardizing manufacturing processes is another key element within Six Sigma. Standardization minimizes variations and ensures consistent quality output across different batches or production lines.
By establishing standard operating procedures (SOPs) and work instructions, companies can maintain control over their processes and reduce unnecessary variations that could lead to defects. This consistency results in predictable outcomes while also streamlining training and onboarding processes for new employees.
These process improvement strategies not only provide a systematic approach to problem-solving but also contribute significantly to enhancing operational efficiency and product quality within manufacturing environments.
Following these comprehensive strategies, it becomes apparent that reducing waste within manufacturing processes yields far-reaching benefits that extend beyond just cost-cutting measures.
Impact of Reducing Hidden Factory Waste
The benefits of reducing hidden factory waste through Six Sigma methodologies are numerous, with direct and substantial impacts on a company's productivity, cost structure, and the quality of its products.
Increased Productivity
Implementing Six Sigma principles leads to streamlining processes and operations, reducing waste, and improving overall efficiency. By focusing on minimizing variation and eliminating defects, companies can enhance their productivity and throughput. This is akin to removing roadblocks in a pathway, allowing for smoother and quicker progress. The systematic identification and elimination of inefficiencies pave the way for a more optimized workflow, boosting the overall productivity of the manufacturing process.
Cost Reduction
One of the most significant advantages of implementing Six Sigma is the potential for substantial cost reduction. By identifying and addressing hidden factory waste, companies eliminate inefficiencies and defects that contribute to increased operational costs. With a reduction in rework, scrap, and other unnecessary expenses, the result is improved profitability. These savings extend beyond the direct cost of materials, encompassing labor costs, energy utilization, and more. Essentially, reducing hidden factory waste revolves around maximizing value while minimizing unnecessary expenditure.
Enhanced Quality
Improving process control and reducing defects are essential elements of Six Sigma methodology. As companies implement Six Sigma practices to root out hidden factory waste, they are concurrently enhancing the quality of their products. This directly impacts customer satisfaction and loyalty, as higher-quality products result in increased trust and confidence from consumers. By systematically analyzing, identifying, and resolving issues that lead to defects or inconsistencies in manufacturing processes, companies ensure that their products meet stringent quality standards. By eliminating wasteful practices, companies can uphold greater consistency and reliability in the goods they offer.
The effective implementation of Six Sigma methodologies not only yields quantifiable benefits such as increased productivity, cost reduction, and enhanced quality but also fosters a culture of continual improvement within organizations.
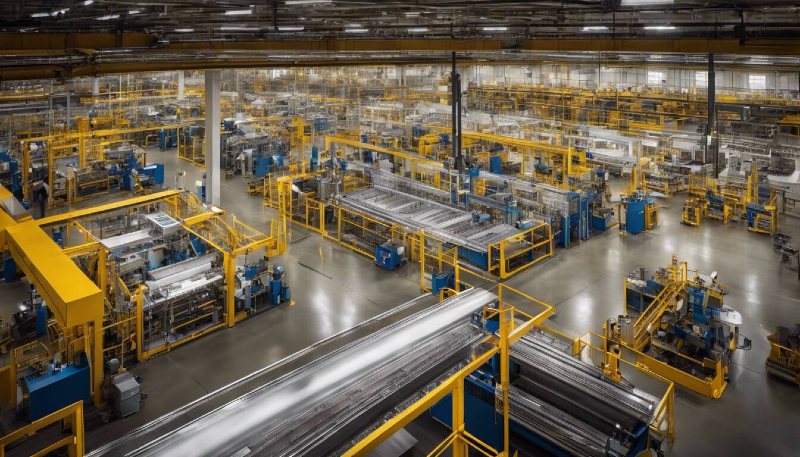
Six Sigma Hidden Factory Manufacturing Band
Relevant Case Studies on Six Sigma
One standout example is GE Aviation, which employed Six Sigma to improve its manufacturing processes. By scrutinizing every detail of their operations, they identified and rectified inefficiencies that resulted in significant cost savings and a noticeable boost in quality. Through these efforts, they were able to drastically reduce rework costs by more than $180 million annually.
Moving from aerospace to healthcare, Johnson & Johnson utilized Six Sigma strategies to streamline their supply chain processes and enhance their operational capabilities. The results were transformative—they achieved sizable reductions in costs and witnessed a notable improvement in product safety and quality.
Similarly, Toyota has long been regarded as an industry leader in operational excellence, and their adoption of Six Sigma principles has only fortified this position. By meticulously identifying and eliminating waste from their production line, Toyota has continuously optimized their processes, leading to heightened customer satisfaction and increased profitability.
Furthermore, General Electric (GE) adopted Six Sigma to address issues within its various business units. One remarkable outcome was seen within their Energy Division, where a focused approach on reducing defects led to a significant increase in revenue—lower prices enabled them to garner more business and ultimately surpass their profit expectations.
These cases underline the diverse sectors in which Six Sigma has proven instrumental. It’s not just limited to one type of industry—the methodology has demonstrated its efficacy across manufacturing, healthcare, automotive, and aviation - showcasing its versatile nature.
Each of these real-life examples underscores how implementing Six Sigma methodologies can result in measurable benefits across different industrial domains. They serve as compelling testaments to the versatility and effectiveness of Six Sigma in driving meaningful improvements in efficiency, quality control, and overall customer satisfaction.
The Future of Six Sigma in Efficiency and Quality Control
Six Sigma has been a game-changer in manufacturing processes, sparking notable improvements in efficiency and quality control over the years. But as technology continues to advance, it's crucial for Six Sigma to adapt and integrate these innovations to further enhance its impact.
One of the most significant trends shaping the future of Six Sigma is the integration of emerging technologies such as Artificial Intelligence (AI) and Internet of Things (IoT). AI offers the capability to analyze massive datasets to identify patterns, predict outcomes, and optimize processes in real-time. This can significantly bolster the predictive and prescriptive analytics central to the Six Sigma methodology, allowing for more proactive problem-solving and decision-making.
When it comes to IoT, it enables interconnected devices to communicate and share data, creating a wealth of information that can be leveraged to streamline operations and identify areas for improvement with greater precision. This connectivity enhances data collection, analysis, and monitoring, reinforcing the foundation of data-driven decision-making inherent in Six Sigma.
Furthermore, digital transformation plays a pivotal role in the evolution of Six Sigma. With the rise of Industry 4.0, manufacturing environments are becoming increasingly automated and interconnected. Lean Six Sigma is likely to be integrated into digital transformation efforts, leveraging automation, AI, and data analytics to drive process improvement initiatives in smart factories with enhanced efficiency and reduced waste.
As industries continue to evolve, sustainability is emerging as a critical focus area. Lean Six Sigma can play a vital role in driving sustainability initiatives by reducing waste, optimizing resource consumption, and improving supply chain sustainability. The principles of Lean Six Sigma can serve as a cornerstone for developing eco-friendly production processes aligned with environmental stewardship.
Continual adaptation and innovation will be essential for Six Sigma's continued relevance. It must remain flexible and responsive to industry trends and challenges while preserving its core principles of process improvement and customer satisfaction.
The integration of AI, IoT, and digital transformation into Six Sigma not only promises heightened operational efficiencies but also paves the way for more sustainable manufacturing practices. The future landscape of efficiency and quality control will undoubtedly be shaped by these advancements as they converge with the foundational principles of Six Sigma.
The journey toward greater efficiency and quality control continues with Six Sigma leading the way, evolving alongside advancements in technology to meet the ever-changing demands of modern industry.
What are some common indicators or signs that suggest the presence of a hidden factory in a process?
Answer: Some common indicators or signs that suggest the presence of a hidden factory in a process include excessive rework, high levels of scrap or waste, frequent equipment breakdowns, and long cycle times. These can be supported by statistics such as low first-pass yield rates, a high number of customer complaints, and increased costs due to rework or scrapped products.
What are the primary causes or factors that contribute to the development of a hidden factory?
Answer: The primary causes of a hidden factory include poor process design, inadequate training, lack of standardized procedures, and ineffective management. These factors contribute to errors, rework, and inefficiencies that lead to the creation of a hidden factory. According to a study by Forbes, businesses waste an average of 20-30% of their total capacity due to hidden factories, resulting in significant financial losses.
How can organizations identify and eliminate the hidden factory to improve productivity and reduce costs?
Answer: Organizations can identify and eliminate the hidden factory by implementing the principles of Six Sigma, which focuses on reducing defects and improving efficiency. By using data-driven analysis and process improvement techniques, organizations can identify bottlenecks, waste, and errors that contribute to the hidden factory. For example, a study by the International Six Sigma Institute found that companies utilizing Six Sigma methods experienced an average cost reduction of 22% and a 28% increase in productivity.
How does the hidden factory impact operational efficiency and overall performance in an organization?
Answer: The hidden factory negatively impacts operational efficiency and overall performance in an organization by introducing inefficiencies, wastes, and rework. It hides within the processes, particularly in areas without proper quality control measures, leading to increased costs and reduced productivity. According to recent studies, organizations can experience up to a 20% loss in operational efficiency due to the hidden factory (Source: Journal of International Six Sigma Institute). By implementing Six Sigma methodologies to uncover and eliminate the hidden factory's defects, organizations can significantly enhance their efficiency and performance.
What is the definition and origin of the term "hidden factory" in the context of Six Sigma?
Answer: The term "hidden factory" in the context of Six Sigma refers to the inefficiencies and waste that exist within a company's processes, but are often overlooked or not fully understood. Originally coined by quality expert H. James Harrington, the hidden factory represents the cumulative effect of errors, rework, scrap, and other non-value-added activities that hinder productivity and quality control. According to a study conducted by the International Six Sigma Institute, the hidden factory can lead to losses of up to 20-30% of revenue for companies. The concept emphasizes the need for organizations to identify and eliminate these hidden inefficiencies through Six Sigma methodologies to improve overall efficiency and quality control.
Recap for Six Sigma Hidden Factory
In the quest for operational excellence, the identification and elimination of the hidden factory are paramount. The hidden factory refers to the inefficiencies, defects, and deviations that occur within a process but go unnoticed, resulting in wasted resources and compromised quality. At the heart of Six Sigma lies the commitment to pinpointing the root cause of such issues, ensuring that solutions are not merely superficial workarounds but comprehensive measures that enhance efficiency and quality control.
To uncover the hidden factory, Six Sigma employs a rigorous methodology that involves meticulous measurements and data analysis. The process begins by assembling a cross-functional team of experts who collaboratively analyze every aspect of an activity. By utilizing lean measurement techniques, these teams can identify deviations from the standard and root causes that may have previously eluded managers and operational teams. This data-driven approach not only reveals the inefficiencies but also allows for the implementation of targeted solutions that address the core issues, leading to sustainable improvements.
Managers play a crucial role in the Six Sigma process, guiding teams through the identification and resolution of hidden factory problems. Their leadership ensures that the solutions implemented are not mere quick fixes but comprehensive measures that transform the way activities are carried out. The incorporation of lean principles emphasizes the importance of continuous improvement, urging teams to revisit and refine processes regularly. By fostering a culture of continuous improvement, Six Sigma empowers organizations to stay vigilant against the re-emergence of hidden factory issues, promoting sustainable excellence.
In conclusion, Six Sigma's approach to unveiling the hidden factory is a strategic and systematic one. By addressing root causes through data-driven measurements and involving cross-functional teams led by managers, organizations can transform their operational landscape. As we delve deeper into the intricacies of Six Sigma, it is essential for individuals to keep learning and enhancing their knowledge.
To excel in Six Sigma, I encourage you to continue your learning journey and request the free-of-charge Six Sigma book, which will undoubtedly contribute to expanding your expertise and proficiency in this transformative methodology.