Six Sigma Critical Quality Control (CTQ) & CTQ Drilldown Tree
Methodology, Examples, and Implementation
Six Sigma CTQ, short for Critical-to-Quality, hinges on key elements that give a product or service its quality. These are based on customer feedback and form the bedrock of robust process improvements in any organization. The CTQ Drilldown tree then enters the scene as a helpful tool, dissecting these broad consumer needs into precise and measurable features. This is not just about dividing one big task into smaller ones; rather, it's about a significant shift from vague requirements to clear objectives that can be measured and enhanced over time. Right around the corner, you're about to delve into this further.
One example of a CTQ Drilldown Tree for a manufacturing process could include the top-level CTQ, such as "Product Reliability". Then, the drilldown branches may specify elements like "Component Durability", "Manufacturing Precision" and "Performance Consistency" all contributing to the overall quality of the product. By analyzing each branch, specific factors critical to the quality of the product can be identified and addressed within the Six Sigma framework.
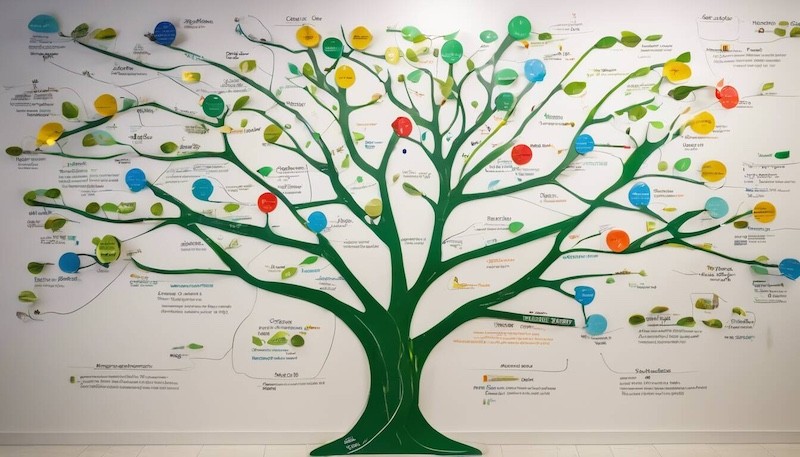
Six Sigma CTQ Drilldown Tree
Six Sigma CTQ: A Broad Look
Imagine buying a new phone and finding out that the battery doesn't last as long as expected. Or ordering a dress online that doesn't fit quite right. These are examples of not meeting
customer requirements, which is exactly what Six Sigma CTQ (Critical-to-Quality) is all about - understanding what's important to the customer.
In Six Sigma, CTQs define the crucial characteristics of a product or service that directly affect its quality. They are the specific attributes, features, or parameters that are most important to the customer. Think of CTQs as the non-negotiable aspects that must be met for the product or service to be considered high-quality.
What is Critical to Quality (CTQ)?
Critical to Quality (CTQ) is a fundamental concept within the Six Sigma methodology, playing a pivotal role in ensuring project success and customer satisfaction. CTQ represents the specific attributes or characteristics that are deemed crucial from the perspective of the customer. The identification and understanding of CTQ are integral to meeting customer expectations and aligning project outcomes with the Voice of the Customer (VOC). In essence, CTQ serves as the bridge between the project goals and the customer's needs.
The goal of defining CTQ is to establish clear and measurable performance requirements that directly contribute to the overall quality of the deliverables. These performance requirements are often referred to as quality drivers, as they are the key factors that drive customer satisfaction. By identifying the drivers through a meticulous process, the project team can ascertain the critical aspects that require focused attention and improvement.
The purpose of the CTQ drilldown tree is to systematically break down these critical factors into more granular components. This phase involves a thorough analysis using statistical tools and control charts to delve deeper into the specific elements contributing to the overall quality. The CTQ drilldown tree provides a structured approach to dissect the project's objectives, allowing for a comprehensive understanding of the interdependencies among various components and their impact on the customer's perception of quality.
What are CTQ Properties?
CTQ properties, or Critical to Quality properties, play a pivotal role in the Six Sigma methodology, serving as key determinants of customer satisfaction. These properties are essential characteristics that directly impact a customer's perception of a product or service. Understanding CTQ properties is crucial for organizations aiming to achieve and maintain high-quality standards. The identification and analysis of CTQ properties involve various methodologies and tools, including statistical analysis, surveys, and expert input. Here are some key points regarding CTQ properties:
- Driver of Customer Satisfaction: CTQ properties act as drivers of customer satisfaction, as they directly influence customer perception and preferences.
- Utilization of Statistics: Statistical tools are employed to analyze and quantify the impact of CTQ properties on overall product or service quality.
- Expert Input: In-depth insights from subject matter experts contribute to the comprehensive understanding of CTQ properties, ensuring a holistic approach to quality management.
- Variation Management: CTQ properties help in managing and reducing variation, ensuring consistency in product or service delivery.
- Integration with FMEA: CTQ properties are often integrated into Failure Modes and Effects Analysis (FMEA) to proactively identify potential failure points and address them before they impact customer satisfaction.
Implementing CTQ properties effectively involves establishing robust metrics, creating a CTQ drilldown tree (CTQ tree), and incorporating them into the overall Six Sigma model. This meticulous approach ensures that organizations not only meet but exceed customer expectations by focusing on the qualities that matter most to their target audience.
Customer Feedback and Process Improvement
CTQs are identified through extensive customer feedback and analysis. This is key because who knows better about the quality of a product or service than the person who uses it? By understanding what customers truly care about, organizations can focus their efforts on improving those aspects to meet or exceed expectations.
For example, if a company manufactures smartphones, customer feedback might reveal that battery life, camera quality, and software performance are the most critical factors to customers. These become the CTQs that guide the organization's improvement initiatives.
Once these CTQs are identified, they act as guiding principles for process improvements within the organization.
Understanding this fundamental aspect of Six Sigma methodology is essential for organizations striving to enhance their products or services and deliver exceptional quality to their customers.
Delving into the CTQ Drilldown Process
CTQ (Critical to Quality) drilldown tree is a tool that can be used to effectively convert customer’s needs and requirements to measurable product/service characteristics, to establish linkage between Project “Y” & Business “Y” and to bound the project or to make the project manageable.
Below is an example of CTQ Drilldown Tree and their associated measurements for two different processes:
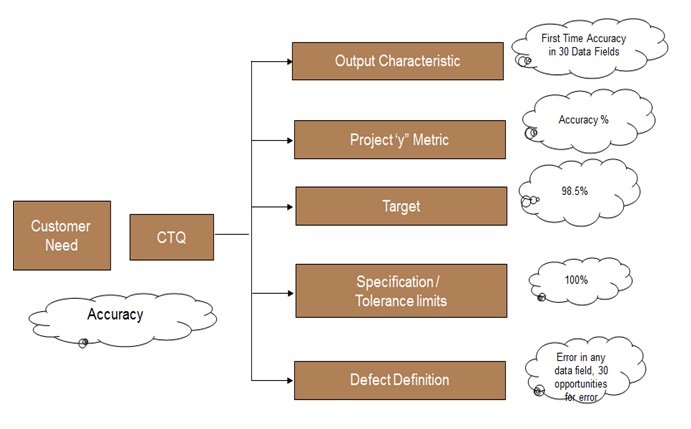
Six Sigma - CTQ (Critical to Quality) Drilldown Tree for Data Entry Application

Six Sigma - CTQ (Critical to Quality) Drilldown Tree for Pizza Delivery Process
The CTQ Drilldown Tree is a significant tool used in Six Sigma. It takes the critical-to-quality (CTQ) elements and dissects them to reveal the specific features or attributes that are most essential to meet customer expectations. Visualize it as a whittling-down process, breaking big, overarching requirements into tiny but important details.
So, let's say our high-level requirement is customer satisfaction. The CTQ Drilldown process helps us identify the specific factors directly influencing customer satisfaction, such as product quality, on-time delivery, and responsive customer service. This structured approach allows organizations to identify the precise aspects of their products or services that need improvement in order to meet or exceed customer expectations consistently.
For example, imagine you're working at a company that produces headphones. A high-level CTQ might be "sound quality." When you drill down using the CTQ Drilldown Tree, you can identify specific attributes related to sound quality, such as bass clarity, noise cancellation effectiveness, and overall volume range. Each of these attributes then becomes a critical factor that needs to be measured, analyzed, and improved to ensure that the final product meets the customers' sound quality expectations.
This process involves a combination of brainstorming sessions and detailed data analysis to identify the root causes of any issues in meeting these specific attributes. By prioritizing improvement efforts based on these findings, organizations can strategically allocate resources and focus on the areas with the most significant impact on meeting CTQs.
Implementing the CTQ Drilldown process requires a methodical approach and the use of specific tools and templates to ensure an effective analysis. Our training materials offer practical guides and templates for implementing the CTQ Drilldown process in your organization. By leveraging these resources, organizations can streamline their efforts and thoroughly evaluate and address all critical attributes identified through the CTQ Drilldown Tree.
Understanding how to navigate the CTQ Drilldown process empowers organizations to uncover the key drivers of customer satisfaction and product quality, enabling them to make targeted improvements that directly align with customer expectations and drive overall business success.
Armed with a newfound understanding of the CTQ Drilldown process, organizations can now unravel practical illustrations that showcase its real-world application and transformative impact.
Practical Illustrations: CTQ Drilldown Tree Examples
Consider walking into a manufacturing facility and witnessing a team huddled around a whiteboard, meticulously mapping out the critical quality characteristics of their production process. This is where the CTQ Drilldown Tree comes into play. Let's consider a specific example to illustrate its application in identifying and analyzing key quality metrics.
In the manufacturing sector, a company using the CTQ Drilldown Tree might focus on pinpointing defect rates, cycle times, and customer satisfaction metrics. By employing this tool, they would be able to drill down into each of these critical quality characteristics to understand their impact on overall process efficiency and customer satisfaction. For instance, they may identify areas where defects are most prevalent and analyze the root causes behind these issues.
Furthermore, the CTQ Drilldown Tree allows the team to prioritize areas for improvement based on their impact on the final product or service. It provides a structured approach to systematically address quality issues and make data-driven decisions.
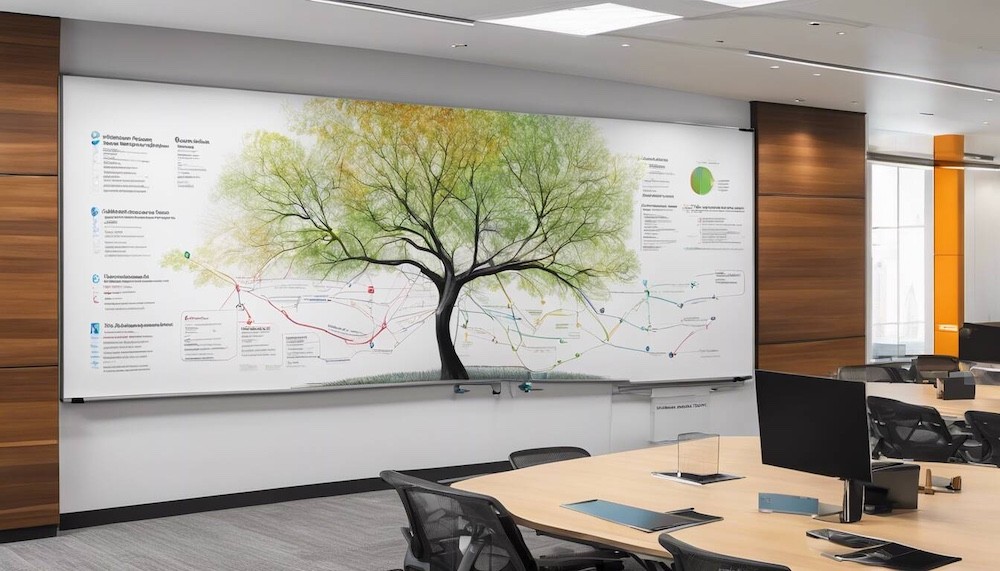
Six Sigma CTQ Drilldown Tree Examples
Moving beyond manufacturing, let's consider another example in the healthcare industry. A hospital using Six Sigma principles might utilize CTQ Drilldown Trees to identify critical quality characteristics in patient care processes. These could include waiting times, accuracy of diagnosis, and patient recovery rates.
For instance, by employing the CTQ Drilldown Tree methodology, hospital staff can delve into wait times for various procedures and diagnostic tests. This analysis can reveal bottlenecks in patient flow, allowing for targeted interventions to enhance efficiency and improve overall patient experience. By drilling down into the factors affecting patient recovery rates, healthcare providers can identify areas for improvement such as post-operative care protocols or rehabilitation programs.
The diverse applications of CTQ Drilldown Trees across different industries exemplify their versatility and effectiveness in addressing critical quality characteristics. Observing these practical examples sheds light on how organizations leverage this methodology to drive continuous improvement and achieve business excellence.
With an understanding of how the CTQ Drilldown Tree methodology can be applied across industries, let's now explore the problem-solving strategies within the Six Sigma framework.
Problem Solving within Six Sigma Framework
In the world of Six Sigma, problem-solving involves more than simply fixing a glitch in the system. It's about understanding why that glitch occurred and creating a solution that prevents its recurrence. The methodology most often used to tackle these problems is called DMAIC, which stands for Define, Measure, Analyze, Improve, and Control. This structured approach ensures that any changes made aren't mere quick fixes but are sustainable improvements.
- Define: The first step revolves around defining the problem in detail. This means not just pointing out a surface-level issue but digging deep to understand its root causes. Think of it as identifying the exact source of an illness before treating it.
- Measure: After defining the issue, it's crucial to measure and collect relevant data to quantify how significant the problem is. This step helps in setting clear goals and identifying performance gaps.
- Analyze: Next comes analyzing the collected data to understand patterns, possible trends, and identify areas where improvements can be made. It's like Sherlock Holmes examining every clue before solving a mystery.
- Improve: Once you have all this information, it's time to devise and implement solutions to address the root causes identified during analysis. This step is all about trial and error, implementing changes and seeing if they work or not.
- Control: The final step is about maintaining the improvement over time. It involves creating systems and processes to ensure that the changes are integrated fully into day-to-day operations.
This methodology provides a systematic way to approach problem-solving so that issues are resolved comprehensively and systematically while also recognizing the importance of tools like root cause analysis and process optimization within the framework.
Problem-solving within Six Sigma isn't just about reacting to issues as they arise. It’s about proactively identifying potential problems—even before they occur—using data-driven methodologies and ensuring continuous improvement becomes a part of everyday practice. This approach not only addresses current concerns but also ensures a resilient and efficient system moving forward.
By utilizing these problem-solving techniques within the Six Sigma framework, organizations can enhance their operational efficiencies, minimize defects, and achieve sustainable results over time.
CTQ Measure: Management and Monitoring
In the world of business, maintaining quality standards is fundamental for customer satisfaction. This is where Critical-to-Quality (CTQ) measures come into play. CTQs are the significant product or service characteristics that satisfy customer requirements and ensure high levels of quality. Now, let's explore the importance of effectively measuring and managing CTQs, as well as monitoring them to continually meet customer needs.
Tracking CTQs enables organizations to stay aligned with customer expectations. Various Key Performance Indicators (KPIs) are used to monitor CTQs and ensure that the critical dimensions of a product or service are consistently met. These KPIs provide valuable insight into the effectiveness of processes in meeting customer requirements, thereby guiding organizations towards continuous improvement.
For instance, if on-time delivery is a crucial customer requirement, organizations can set up KPIs to monitor delivery performance, ensuring that products or services reach customers within the specified timeframe. This level of insight allows businesses to identify areas for improvement and make data-driven decisions to enhance their performance in meeting CTQs.
Establishing an effective CTQ measurement system is a key aspect of implementing Six Sigma methodologies. It involves identifying meaningful metrics that directly relate to customer needs and aspirations. Furthermore, this approach ensures that the organization remains focused on what truly matters to customers, allowing for targeted efforts towards delivering value and satisfaction.
Let's now explore effective strategies for setting up comprehensive CTQ measurement systems within the Six Sigma framework.
Successful Implementation of Six Sigma CTQ & CTQ Drilldown Tree
Implementing Six Sigma CTQ and the CTQ Drilldown Tree isn't just about following steps in a manual; it's about creating a culture of excellence within an organization. The first step to ensure success is to gain commitment from the top leadership. When leaders prioritize quality improvement and set clear expectations for the use of Six Sigma methodologies, it sends a powerful message to every employee in the organization.
Furthermore, effective training is essential. Employees at all levels need to understand how to apply the CTQ and CTQ Drilldown processes to their specific roles, and this requires comprehensive training.
The Online Six Sigma Training Program offers accessible resources for professionals looking to gain expertise in implementing these methodologies. This includes detailed explanations, examples, and multiple-choice test questions to prepare individuals for their Six Sigma Certification Examination.
For instance, Company A reduced customer complaints by 30% after implementing Six Sigma CTQ and the CTQ Drilldown Tree. This success was attributed to thorough training provided to employees at all levels within the company as they worked towards improving product quality and customer satisfaction.
In addition, creating a culture of continuous improvement is crucial for successful implementation. This means encouraging employees to identify opportunities for quality enhancement and empowering them with the tools needed to address those opportunities using the CTQ Drilldown Tree. By fostering an environment where feedback is valued and acted upon, organizations can continuously improve their processes and products.
Our training materials contains best practices and success stories from leading companies which have effectively implemented CTQ and CTQ Drilldown processes. These exemplify the benefits of improved quality, enhanced customer satisfaction, and streamlined processes that result from successful implementation of Six Sigma methodologies.
With these principles in mind, organizations can pave the way for successful implementation of Six Sigma CTQ and the CTQ Drilldown Tree, translating into tangible improvements in quality and customer satisfaction.
In conclusion, embracing a culture of excellence through top leadership commitment, comprehensive training, and a focus on continuous improvement sets the stage for the successful implementation of Six Sigma CTQ and CTQ Drilldown Tree, ultimately leading to enhanced quality and customer satisfaction.
Recap for Six Sigma CTQ & CTQ Drilldown Tree
Six Sigma is a methodology widely employed to enhance process efficiency and product quality. At its core lies the Critical to Quality (CTQ) concept, a crucial element that helps organizations identify and address the specific attributes deemed vital by customers. CTQ Drilldown Tree, an essential tool within the Six Sigma framework, further refines the CTQ approach. It functions as a detailed roadmap, breaking down the critical quality elements identified through CTQ analysis. The drilldown process provides a comprehensive understanding of customer needs and assists in the design and implementation of strategies for continuous improvement.
In the application of Six Sigma, Quality Function Deployment (QFD) plays a pivotal role in translating customer needs into specific product or service characteristics. The CTQ Drilldown Tree aligns seamlessly with QFD, acting as a visual representation that guides the development process. By employing a diagrammatic approach, organizations can systematically identify and prioritize customer needs, ensuring that their products not only meet but exceed customer expectations. This alignment is crucial for maintaining high-quality standards and delivering products that resonate with the market.
As organizations delve into the intricacies of Six Sigma CTQ and CTQ Drilldown Trees, understanding the statistical aspects becomes imperative. Standard deviation, a measure of variation, plays a key role in gauging the consistency of processes and products. Technology development, in conjunction with Six Sigma methodologies, allows organizations to harness ways to get data-driven insights for optimal decision-making.
To further explore these concepts and deepen your understanding of the Six Sigma framework, the International Six Sigma Institute offers a free-of-charge Six Sigma Framework book. For those who are eager to enhance their knowledge and proficiency in Six Sigma, this valuable resource provides a comprehensive guide to implementation and continuous improvement. To embark on your journey of mastering Six Sigma, request and download the book today.